The coming of the New Year brings a boatload of good news for the Bay Bridge East Span replacement project.
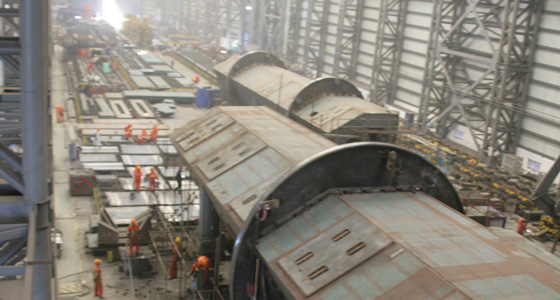
Segments of the iconic tower for the self-anchored suspension bridge are fabricated in a giant hangar-like building at the ZPMC facility near Shanghai. Photo by Bill Hall
By John Goodwin
Published: January, 2010
The coming of the New Year brings a boatload of good news for the Bay Bridge East Span replacement project. The first steel bridge deck sections for the signature self-anchored suspension (SAS) portion of the new bridge have now been loaded aboard a ship in China, with the vessel scheduled to begin its month-long voyage across the Pacific before Bay Area revelers start singing “Auld Lang Syne.”
“Team China is firing on all cylinders,” said Ken Terpstra, Caltrans’ project manager for the Bay Bridge East Span replacement project, as he reflected on the fabrication of steel components for the SAS. Acknowledging that the first shipment is leaving China more than a year behind the original schedule, Terpstra explained the enormity and intricacy of the SAS project — which presented complex design and fabrication challenges — and the exacting quality standards established for the finished pieces. “The standards for bridges are higher than for virtually any other type of steel structure.”
Based at the sprawling Shanghai Zhenhua Heavy Industry Co. (ZPMC) complex on Changxing Island in the Yangtze River near Shanghai, Team China includes more than 2,000 local welders, grinders, carpenters, sweepers, safety monitors, forklift drivers, foremen, data-entry clerks and others. The team also includes scores of workers from the prime contractor on the SAS project, a joint venture known as ABF formed by American Bridge Co. and Fluor Corp., plus dozens of Caltrans staff members, quality inspectors from Upland, Calif.-based Caltrop Corp., and various stateside construction management specialists, designers and consultants.
While American fabrication plants account for the bulk of the steel to be used in the new East Span, the effort to complete the entire bridge is a truly global enterprise. Major components are being designed or manufactured in 11 U.S. states and seven different countries, including Canada, Japan, Norway, South Korea, Taiwan and the United Kingdom as well as China. Bay Area fabrication sites include Antioch, Campbell, Fairfield, Livermore, Napa, San Francisco and Vallejo.
At the ZPMC facility on Changxing Island, the fabrication takes place in more than a dozen blue steel warehouses. Typically measuring 360 meters by 60 meters, the hangar-like “fabrication bays” are dedicated to particular elements of the SAS project. Some bays are used solely to assemble pieces of the iconic 525-foot-tall tower. Other bays focus on welding steel plates atop support sections known as U-ribs to create segments of the span’s road deck. And there are OBG bays, where a total of 86 gigantic box girders that will form the bridge superstructure are put together, forming 28 separate segments of between two and five box girders each.
“There’s a documentation process, known as ‘green tagging’ in place,” explained Bay Area Toll Authority consultant Ted Hall, noting that inspectors literally are affixing green decals to pieces of steel to certify their compliance with contract specifications and quality standards. “The green tagging process ensures that all welds have been completed in accordance with the contract specifications, and it enables us to provide documentation for the completion of all welds. Documentation also provides an important record for future bridge maintenance requirements.”
The green tagging process is more than a bit reminiscent of prenatal care. Just as medical technicians use ultrasound to probe fetal health and development, welding technicians employ Phased Array Ultrasound Technology (PAUT) to probe the quality of welds. And the tools are nearly identical, right down to the bottle of viscous conducting goo and stethoscope-like monitoring instruments.
“It’s no mean feat to convert plates of steel into the intricate components that will make up the SAS,” commented Terpstra. “But our team is doing it right and we’re doing it faster all the time. Once that first ship arrives in the Bay around late January, the next should be just a couple months behind. As the first steel deck and tower sections are lifted into place, 2010 will be the year the new bridge really starts taking shape.”
John Goodwin is a Public Information Officer for the Metropolitan Transportation Commission and the Bay Area Toll Authority.
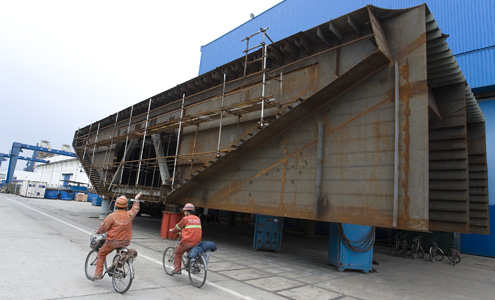
ZPMC workers pedal past an orthotropic box girder section that will form part of the bridge superstructure. Photo by Lucas Schifres

Left: With the first legs of the SAS tower looming in the background, a trio of Team China members stands dockside beside an orthotropic box girder segment ready for shipment. Right: A giant barge-mounted crane prepares to lift a section of the new bridge onto the ship for transport to San Francisco Bay. Photos by Lucas Schifres