In October, the heavy lift vessel Tern arrived in San Francisco and picked up the Port of San Francisco’s Drydock #1 for towing to a green-certified ship recycling facility near Shanghai, China.
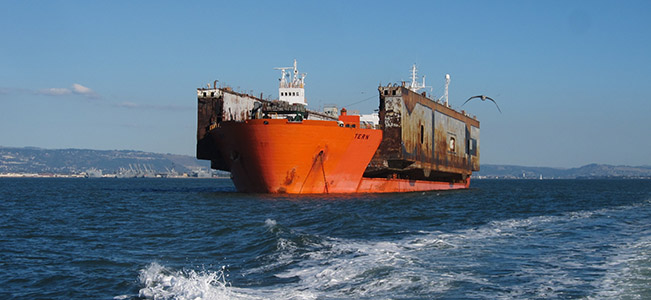
Photo by Frank van Hoorn
BC Staff Report
Published: November, 2014
In October, the heavy lift vessel Tern arrived in San Francisco and picked up the Port of San Francisco’s Drydock #1 for towing to a green-certified ship recycling facility near Shanghai, China. The drydock’s departure represented the last phase of 15 years of efforts to find a final resting place for Drydock #1, which was declared unfit for service in 1999.
An Eventful Day
Tern is a semi-submersible heavy lift vessel, which means that it partially sinks itself so that cargo may be floated over its cargo deck. She then de-ballasts to lift the cargo out of the water to complete the heavy lift operation.
Tern lifted the 4,200-ton Drydock #1 out of the water on Saturday, October 18 at approximately 9:00 a.m.
Two unexpected events made the operation even more complicated than planned. First, as reported by several local media outlets, human remains surfaced during the operation as the drydock was being towed.
“When I was called over to the aft of Drydock #1 midway through the tow to see what appeared to be a decomposed body that surfaced, I instructed the tug crew to secure the remains and cut the tug engines right away,” said Daley Dunham, who manages special projects for the Port of San Francisco. “We basically suspended this whole carefully orchestrated operation that had been in the works for a very long time. We wanted to do as much as we could to preserve the remains.”
However, Dunham reported, despite the crew’s best efforts, the body disappeared back underwater and did not resurface.
Dunham also said that the drydock itself was not without surprises. “We had operated using the best information we had, but as it turns out, once they completed the lift, we realized that someone along the line had made some modifications that changed the underbelly of the drydock a little bit,” said Dunham.
“This was key because the cradling system installed on board the Tern was custom engineered for the drydock in order to distribute its weight evenly. It was touch-and-go there for a little bit, but ultimately they decided it was a go.”
Dunham reported that, after a couple of days of sea fastening, Tern departed on October 22 for the recycling facility near Shanghai.
History of the Drydock
Drydock #1 was constructed for the Navy in 1942 for the purpose of constructing and repairing military vessels. Operated at Pier 70 by Bethlehem Steel (later by Todd Shipyard) with other military assets, it was part of one of the largest domestic shipbuilding efforts for World War II. Navy contractors used Drydock #1 exclusively for that purpose until the late 1960s. As use of the drydock began to diversify, Pier 70 operators began servicing non-military vessels, participating as a commercial enterprise in the ship repair market until the late 1990s.
In 1987, the Port of San Francisco acquired Drydock #1 through Todd Shipyard’s bankruptcy proceedings. For the next 12 years, Drydock #1 remained in operation and in the custody of the port’s Pier 70 tenant. In 1999, the drydock revealed signs of extreme wear and tear and was removed from service. At that time, the port sought out a replacement drydock, ultimately acquiring the U.S. Navy surplus drydock Steadfast (renamed Eureka).
The Port’s Efforts to Dispose of Drydock #1
In 2000, the port offered Drydock #1 for auction, hoping to sell the salvage rights of the asset. However, it became clear that the winning bidder did not have the resources necessary to remove Drydock #1 from port property and take possession of it and, as part of a claim settlement, the transaction was cancelled.
In 2002, the port again put Drydock #1 up for auction. This time, the bids received had a negative value. As the surprising complexity of disposal of Drydock #1 became apparent to port staff members, it also became apparent that disposal would be an expensive proposition. This could not have been more evident than on November 7, 2002, when Drydock #1 broke loose of its moorings in severe winds, floated out into the Bay and ran aground on Yerba Buena Island, costing the port $1.7 million.
There were several more attempts by port staff to enter into a contract for disposal of Drydock #1 over the remainder of the decade, all of which resulted in unsuccessful partnerships with responders ultimately incapable of properly handling disposal.
The Final Resting Place
In 2010, the Department of Defense selected the salvage arm of the U.S. Navy to administer the current project, which has now come to fruition. Under the supervision of the Navy, a contractor skillfully removed the end section wing walls, separated the bow and aft sections, and landed each in turn at the slipway at Pier 70, where demolition could be conducted in a contained cell. All activity was closely monitored and approved by port environmental staff. This demolition, remediation, recycling and site restoration was completed in October 2013 at a total cost of just under $3.2 million.
The port then engaged Dockwise, a Dutch-held global marine heavy-lift and transport company with U.S. headquarters in Houston, to lift and transport the drydock. Dockwise operates the largest fleet of specialized vessels in the world, consisting of 25 semi-submersible heavy transport vessels.
Although the port’s obligations ended once the lift operation was completed (defined as the deck of the lift vessel breaking the surface of the Bay), the port made an additional condition of sale that Dockwise provide the port with a certificate of proper disposal upon conclusion of the ensuing ship recycling operation.
The certificate of proper disposal will be provided by Sea2Cradle, a third-party environmental organization that specializes in monitoring the decommissioning, breaking, remediation and recycling of large seagoing vessels to ensure compliance with the highest international standards.
“I want to make clear that this is not a low wages, lax environmental standards in China story,” said Dunham. “The scrapyard that it is going to in China is one of the most advanced ship recycling facilities in the world.”
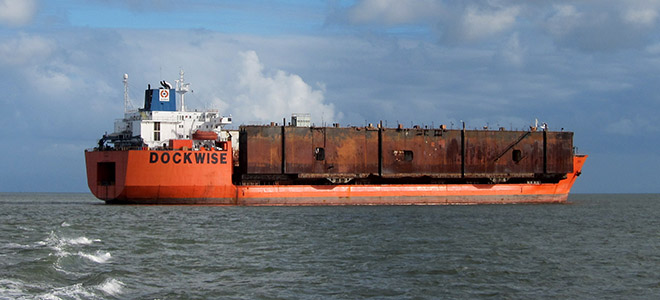
After Drydock #1 was loaded on to the semi-submersible Tern, she then de-ballasted to lift the cargo out of the water to complete the lift operation. Photo by Frank van Hoorn
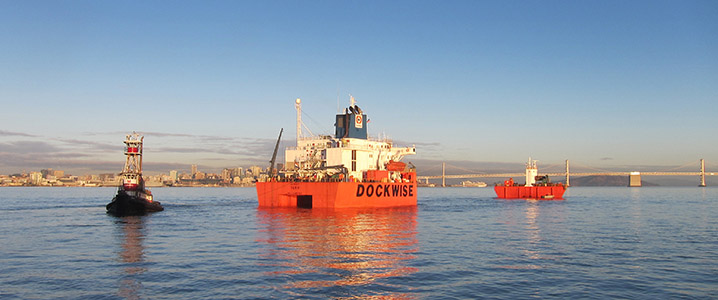
The lift vessel Tern is partially submerged in preparation for loading Drydock #1. Photo by Frank van Hoorn