The cost of the new Martinez Bridge has swollen to over $1 billion dollars, due to fish mitigation, weak sub-structure rock, and building material cost increases.
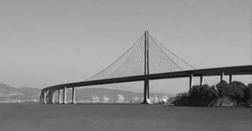
By Guy Span
Published: June, 2004
The cost of the new Martinez Bridge has swollen to over $1 billion dollars, due to fish mitigation, weak sub-structure rock, and building material cost increases. This raised the estimates from a 2001 view, which priced the bridge at $652 million. To pay for the increased costs, its looks as if Caltrans will have to reach into the RM-2 funds and grab some $400 million that might have been spent on other transit relief projects. But that blow out is peanuts compared to the new Oakland Bay Bridge, which Caltrans had hoped would be in the $740 million range.
When the bids were opened on May 27, there was just one bidder, a consortium that included the American Bridge Company. Per the bidding rules, there were two bids, one with domestic and the other with foreign steel. The foreign steel option came in at $1,398,776,550 and the domestic steel was $1,803,771,050. So a $740 million self-anchored suspension bridge will now be $1.8 billion project, before cost over runs.
So how is this possible? Bay Crossings asked a local builder why these projects were getting so expensive. He declined to give his name, saying, “I’ll just sound like a whiner,” but he did give some fairly startling facts. Rebar, a basic metal component for concrete construction was selling for 8 cents a foot last year and now goes for 40 cents a foot. He expects it to hit a dollar and noted the big guys are starting to hoard this stuff.
OSB Plywood (structural grade) has increased from $11 to $27 while regular plywood is up about 50 percent and steel of any kind is hard to get. So our builder was not at all surprised by the higher bridge costs. And Caltrans shouldn’t be either, as their own Price Index for Selected Highway Construction Projects for the quarter ending March 31st is up 140.7 percent.
So Bay Crossings asked our builder to speculate on why the basic building material cost was so high. He gave two reasons, suggesting that the rebuilding of Iraq was consuming a lot of material, as was the huge economic growth in China, which also has been blamed for high oil prices, as their economy consumes more energy. Whatever the cause, Bay Area residents will end up paying a lot more to have things built. And the bigger it is, the more they will pay.
You can contact Guy Span at info@baycrossings.com.